AGA
Project brief
For almost
a century AGA has brought to life the kitchen by designing, manufacturing and
installing premium quality kitchen equipment including its iconic range
cooker.
“At AGA it is our
aim to make life good through thoughtful design.
We create and curate products that offer tangible solutions to help people live their best lives. Put simply, everything we make is designed to make things easier, more efficient and better all round.”
With the above statement ever present in mind, the client approached us with an issue which was not sitting correctly with their philosophy, their packaging. The manufacturing site at Telford was becoming more and more efficient and with worldwide delivery becoming more and more the norm, they were finding that their current packaging was taking too long to pack, had too many pieces associated with it, and wasn’t actually protecting the valuable cookers as it should.
When the client approached us with this challenge, we started the project from the ground up. Completing on-site audits, following the manufacturing process from start to finish, completing time trials, and assessing the materials currently used, we felt a whole new approach was required. The current packaging was massively time-consuming and consisted of 32 parts just for the external of the cooker. Even with so many parts there were gaps where the cooker was exposed and if elements were not fitted correctly, key areas would be vulnerable in transportation.

Design and Development
What we created was a streamlined “bubble” around the cooker, consisting of far fewer parts and offering 100% coverage of the product. The main part of the packaging is a one-piece air sleeve that protects the four sides of the cooker. The sleeve can be inflated prior to packing or on the cooker itself.
An air U shape is also added to sit on top of the cooker and offer further layers of protection to the front and rear. Packing time was reduced from 15mins to just 5 minutes and the number of total external parts was reduced from 32 to 8!
The previous pack was heavy, with multiple foam fitments that were bulky to store and difficult to dispose of. The air sleeves we created meant a reduction in overall packaging weight of 2.8kg per cooker, a reduction of 15.5%. The air sleeves are stored flat showing a huge saving on pallet spaces. Due to the nature of the previous fitments, they would become damaged in transit and installation and with so many pieces to collect up, were rarely re-used. The new air sleeves make the removal of the packaging very quick and with a massively reduced inventory of parts is much more easily returned to the factory to be re-used.
With this bespoke unique solution to AGA's problem, it is felt now that the packaging reflects their own philosophy of design and presentation with all the below benefits to boast about too.
Images
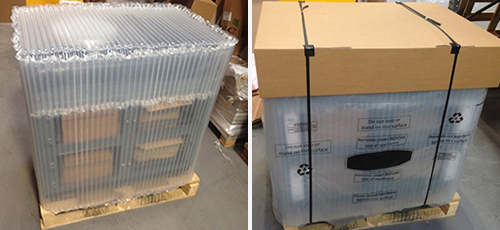